How to Implement an Effective Factory Maintenance Plan: A Guide
Factory maintenance, often referred to as industrial or plant maintenance, is a crucial aspect of running a successful manufacturing operation. This involves a set of planned actions aimed at keeping machines and processes operating at their optimal capacity.
Routine maintenance not only extends the lifespan of machinery but also increases safety, productivity, and efficiency – all vital factors that directly impact a factory’s bottom line.
Poor maintenance can lead to unnecessary downtime, costly repairs, and a drop in overall productivity. Therefore, implementing an effective factory maintenance plan is an essential strategic move for any manufacturing entity.
This guide aims to provide insights and strategies on how to establish such a plan, ensuring your factory operates smoothly and remains competitive in the rapidly evolving manufacturing landscape.
Identify Maintenance Needs
Every piece of equipment in your factory has specific maintenance requirements. Identify these needs by thoroughly understanding the manufacturer’s guidelines, studying the equipment’s history, and analyzing any recurring issues.
For example, should you contact fabricators like www.tigermaterialhandling.com/ or other maintenance service providers as and when needed?
Or would it be more beneficial to invest in a preventive maintenance program that includes regular check-ups and inspections by professionals? Factory maintenance needs vary, and it is up to the management to assess them accurately.
Even if your factory maintains a mix of new and old machinery, it is essential to tailor the maintenance plan to cater to each piece of equipment’s unique needs. While it may seem like a daunting task, proper maintenance scheduling allows for better resource allocation and helps prevent unexpected breakdowns.
Develop a Maintenance Schedule
Structure your maintenance activities on a schedule. This could be time-based or condition-based. Remember, the goal is to minimize unexpected breakdowns and maximize equipment life. Time-based maintenance involves scheduling routine inspections, lubrication, cleaning, and other tasks at specific intervals.
💥🎁 New Year & Easter Deals On Amazon !
Don't miss out on the best discounts and top-rated products available right now!
🛒 Shop Now and Save Big Today!*As an Amazon Associate, I earn from qualifying purchases.
In contrast, condition-based maintenance relies on the equipment’s performance metrics to determine when it needs attention. By setting a schedule, you ensure that all machinery is regularly checked and maintained before any major issues arise.
Furthermore, a maintenance schedule allows for better planning and allocation of resources, reducing the chances of downtime due to the unavailability of materials or personnel. For instance, if you have a large factory, it may be more efficient to divide maintenance tasks into zones and rotate them throughout the year.
Even hiring a dedicated maintenance team or outsourcing to a reputable service provider may be necessary, depending on your factory’s size and needs.
Train Your Staff
Ensure that your maintenance team is properly trained and equipped to handle the tasks at hand. They should understand the comprehensive maintenance plan and know how to troubleshoot common problems. Employees should also be aware of safety protocols and procedures, as well as any potential hazards associated with maintenance activities.
Regular training and upskilling will not only improve the efficiency and effectiveness of your maintenance team but also foster a culture of preventive maintenance within your factory. For larger factories, consider hiring a dedicated maintenance manager to oversee and coordinate all maintenance activities.
Most employees do not have the expertise or time to handle maintenance tasks on top of their regular duties, making a designated manager a valuable asset. However, ensure that the maintenance team is still involved and aware of all activities to maintain a sense of ownership and responsibility.
Invest in a Maintenance Management System
Computerized maintenance management systems (CMMS) help automate, streamline, and quantify maintenance operations. These systems can assist in scheduling, tracking, and analyzing maintenance tasks, leading to higher efficiency and reduced costs. T
hey also provide real-time data on equipment performance, allowing for timely and informed decision-making. CMMS systems can range from simple spreadsheets to complex software solutions. Choose one that best fits your factory’s needs and budget.
Furthermore, regular updates and maintenance of the system itself are crucial in ensuring its effectiveness. These systems are an invaluable tool for maintaining a detailed record of maintenance activities, which can come in handy during audits or compliance checks.
Over time, the data collected can also provide insights into potential areas for improvement. Many CMMS systems also offer mobile applications, allowing for on-the-go maintenance tracking and updates.
💥🎁 New Year & Easter Deals On Amazon !
Don't miss out on the best discounts and top-rated products available right now!
🛒 Shop Now and Save Big Today!*As an Amazon Associate, I earn from qualifying purchases.
Prioritize Safety
Ensure regular safety checks, and training, and strictly adhere to all safety standards and regulations. Maintenance activities can involve hazardous tasks, and neglecting safety protocols can lead to accidents, injuries, or even fatalities. Safety should be a top priority in all maintenance operations.
Additionally, providing personal protective equipment (PPE) and implementing proper lockout/tagout procedures can further mitigate any safety risks. The PPE should be regularly inspected and replaced when needed, and all employees should receive proper training on how to use them.
For instance, eyewear and gloves are critical for protecting against potential hazards such as chemical spills or debris from machinery. In addition, employee training should include emergency protocols in case of any accidents or incidents.
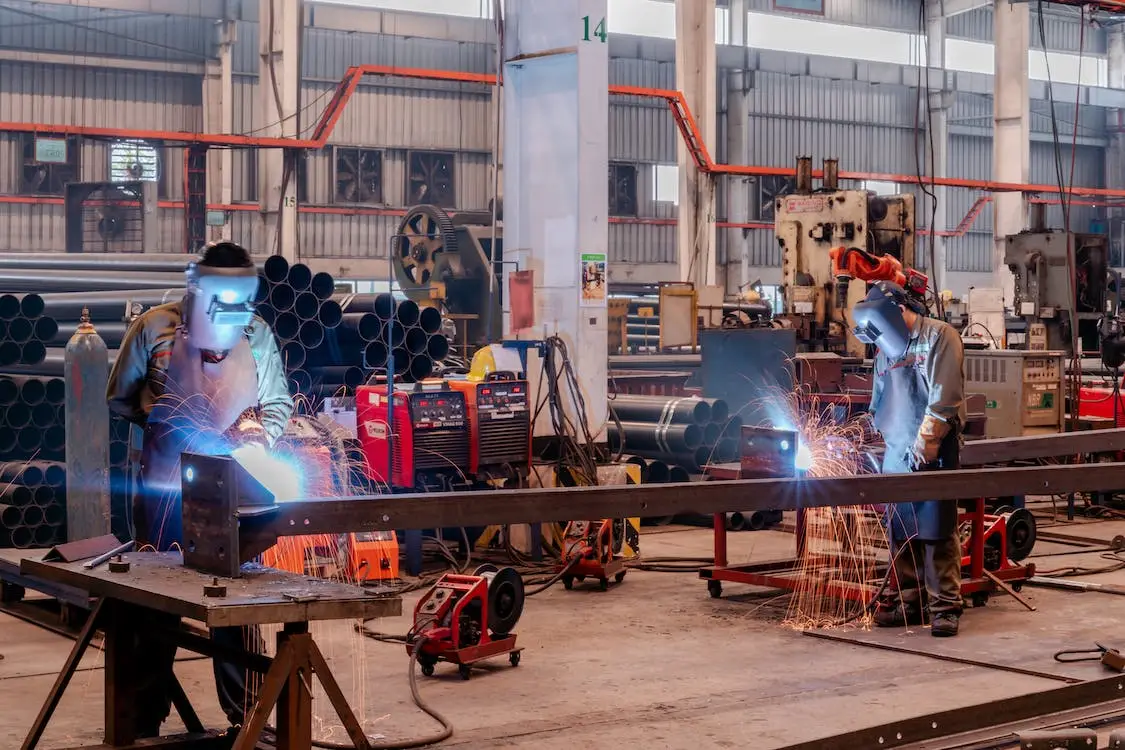
Review and Adjust the Plan Regularly
An effective maintenance plan is not static. It should be regularly reviewed and adjusted based on the evolving needs of the factory, changes in technology, and feedback from the maintenance team. Keeping your plan up to date ensures that it remains relevant and effective in optimizing equipment performance.
Additionally, regularly reviewing the plan can help identify any potential gaps or areas for improvement. The review should also involve analyzing maintenance data and identifying trends or patterns that could indicate underlying issues.
For example, recurring breakdowns in a specific machine may indicate the need for more frequent maintenance or replacement. If necessary, don’t hesitate to make adjustments and improvements to your plan to ensure its effectiveness. After all, the goal is to continually improve and optimize your factory’s maintenance processes.
By identifying maintenance needs, developing a schedule, training staff, investing in a management system, regularly reviewing the plan, and prioritizing safety, you can establish an effective factory maintenance plan that benefits your factory’s overall performance and success.
Remember, preventive maintenance is always better than reactive maintenance, so don’t wait for equipment to break down before taking action. Start implementing an effective factory maintenance plan today and reap the benefits of a well-maintained operation. Sustainability considerations, such as using energy-efficient equipment and sustainable materials, can also be incorporated into the maintenance plan to support environmental goals and reduce the factory’s ecological footprint.