Quality Circle Process | Quality Circles Advantages and Disadvantages
Quality Circle Definition
A Quality Circle is a group of people in an organization who meet regularly, usually once a month, to share ideas about improving the quality of work life.
Quality Circles are quality improvement groups that focus on the needs and concerns of employees. They are usually composed of 6 to 12 members selected from different work functions and levels within an organization.
The goal is to improve efficiency and create a more productive, rewarding environment for all associates. A Quality Circle helps the group members to identify problems within their work environment and work processes, formulate solutions, and implement improvements. They also develop a plan on how to accomplish the changes.
The most basic goal of a Quality Circle is to build a consensus on what needs to be improved in an organization. The purpose is to bring all involved parties together for joint problem solving to lead to more effective operations and more satisfied employees.
What is Quality Circle Process?
The quality circle process is a quality control technique, which originated in Japan. It involves using a committee of workers that analyzes and solves various departments’ quality problems in the organization.
The quality groups are established in every department and trained on problem-solving using statistical quality control and other processes.
They are encouraged to make essential inputs to critical decisions affecting their activities.
Quality circles members are not permanent committees’ members and comprise small groups of about eight to ten company employees, and membership is rotated between members of the department/production plant. They meet together regularly to discuss day-to-day issues such as quality, productivity, and safety, with the object of:
- Making improvements
- Organizing their implementation
History of Quality Circles
The first Quality Circle was established in the United States in 1962 by Ishikawa Kaoru. It was a management technique to improve quality by systematically involving employees in solving problems and identifying new process improvement opportunities.
Quality Circles are an example of employee participation in management. Initially, they were intended to be self-directed work teams that would establish goals and priorities for improvement projects. In this role, the Quality Circle can share responsibility for solving a problem with management.
💥🎁 New Year & Easter Deals On Amazon !
Don't miss out on the best discounts and top-rated products available right now!
🛒 Shop Now and Save Big Today!*As an Amazon Associate, I earn from qualifying purchases.
The Quality Circle Program has been used by many manufacturing companies in the United States and around the world, including several Fortune 500 firms. The technique is widely recognized and supported by American industry associations, including the United States Council for International Business (USCIB).
Quality Circles have been used extensively by Chrysler Corporation since 1979. Chrysler created a comprehensive system of quality programs that support total quality management (TQM). The system included employee, management, and supplier involvement and included the Quality Circle concept. Chrysler’s system of quality programs has been adopted by General Motors and Ford as well by many Japanese companies.
Quality Circles have also been used in education at the elementary, secondary, and higher education levels. The purpose is to improve student learning through problem-solving and classroom process improvement. Quality Circles have been used successfully in K-12 schools in Michigan, Kentucky, Connecticut, West Virginia, Washington DC, California, and elsewhere.
Quality Circles are organizational tools that can improve quality and performance while reducing cost.
By improving the quality of work-life, people can gain satisfaction, loyalty, and commitment to their jobs. They will feel they have a say in decisions affecting them, which will increase their sense of ownership of the organization. Employee’s morale will increase as they see their concerns being addressed and results that benefit them and their organization.
The benefits of Quality Circles are not limited to individual employees. An organization benefits from increased productivity, lower costs, higher morale, better teamwork, worker satisfaction, and retention of quality employees.
Quality Circles are a part of Total Quality Management (TQM). The goal of TQM is to achieve quality improvement throughout the entire organization. Quality Circles are one of the mechanisms for achieving this goal.
Quality Circles Steps
The process of becoming involved in improvements is similar to that of any other team effort.
- First, a group needs to be formed around a common interest or goal. In this case, the goal is to improve quality. The group needs to define its goals and how it will achieve them. The group must establish specific objectives, identify potential obstacles, and discuss strategies for overcoming obstacles.
- The next step is to develop a plan that outlines what needs to be accomplished in order to reach the defined goals. Tactics for accomplishing the plan are then developed. An action plan can be developed with specific “how-to” steps that detail how each tactic will be accomplished.
- The final step in any improvement effort is to take action. Working through a plan ensures that the steps needed for success are followed and that nothing is overlooked.
Structure & Elements of Quality Circle
Structure of Quality Circle
Non-members and members make up the typical structure of quality circles. An organization’s hierarchy is divided into seven levels: non-members, members, leader/deputy leader, facilitator, departmental/steering committee, coordinating agency, and top management.
💥🎁 New Year & Easter Deals On Amazon !
Don't miss out on the best discounts and top-rated products available right now!
🛒 Shop Now and Save Big Today!*As an Amazon Associate, I earn from qualifying purchases.
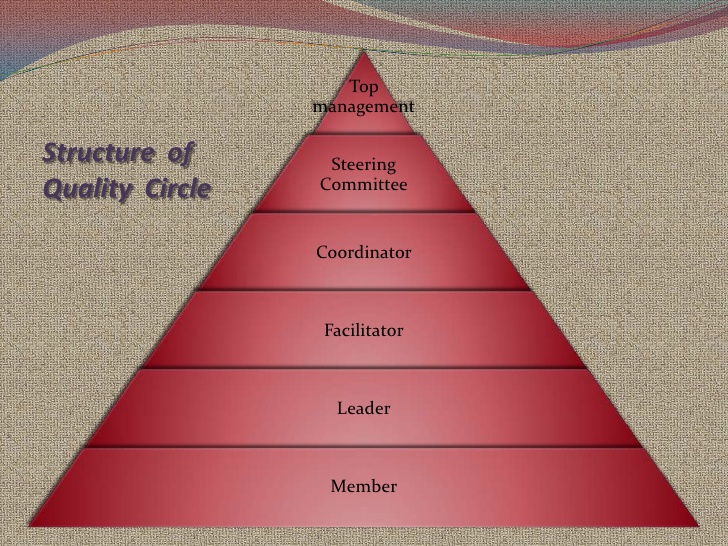
Most people involved in Quality Circles are volunteers. However, the organization may provide training, support, and office space for these employees. Their time commitment is usually limited to one or two hours per month. The rest of their time is spent doing their regular job.
Quality Circles work best when the group members have a common interest in improving the organization. The members must have an understanding of the organization’s goals and how they are achieved. Members usually need at least one or two tasks to perform together in order to feel that they are involved. They also need a way to share information and experiences in order to achieve their common goal.
Quality Circles can be successful when members have an interest in seeing their specific tasks completed. The experience of working together forces group members to solve problems and work through issues that they would not normally face on their own. This helps build a sense of ownership for the work being performed. These activities will help to increase self-confidence, productivity, and motivation.
In order to achieve the desired results, Quality Circles require the involvement of management and supervisors. Management must first make certain that the Quality Circle has what it needs to be successful. This means proper tools and equipment and adequate time for training.
Management should also provide guidance by identifying obstacles and issues that the group will need to address. They can help by providing the information needed to accomplish the task and identifying any resources or experts that might be of assistance.
Supervisors can help with team building, problem-solving, training in teamwork techniques, and leadership skills. They can also become involved in problem-solving and work with their staff members to overcome obstacles. This helps supervisors to build skills in quality improvement and teamwork.
Supervisors must provide the proper resources needed by the Quality Circle. Those resources include time, support, information, people, data, materials, and equipment. Supervisors must also delegate time for training activities such as brainstorming or problem-solving.
They must be open to new ideas and encourage group discussion and participation. They should provide feedback to help the Quality Circle members feel comfortable with their roles.
Group members are usually drawn from the organization. However, they can also be from other organizations that have expertise in a specific area. These experts can help with data collection, analysis, and problem-solving. They are valuable when dealing with problems outside of the group’s expertise or experience.
💥🎁 New Year & Easter Deals On Amazon !
Don't miss out on the best discounts and top-rated products available right now!
🛒 Shop Now and Save Big Today!*As an Amazon Associate, I earn from qualifying purchases.
Essential Characteristics Of Quality Circles.
- Membership is voluntary but usually consists of several company employees and may consist of a mixture of skilled and unskilled employees.
- Each circle selects its own leader, and usually, the organization concerned provides training for such leaders’ inappropriate subjects (discussion leading, quality control, etc.)
- Members are trained in problem-solving, statistical quality control, and working groups. The leader may work with the group, but efficiency experts are usually not excluded from the team. The team members participate actively in solving work-related problems.
- Although the groups were initially trained in analyzing quality problems, other problems like cost reduction, safety problems, employee morale, workshop facilities improvement, pollution control, and education of employees are also dealt with.
- The employees are given the tools, required group support, and opportunities to nip problems in the bud.
- Each Quality Circle is responsible not only for recommending solutions but also for actually implementing and evaluating results.
- The Quality Circle members present their results, reports, and deliberations for consideration by management.
- They usually implement proposals accepted by management.
Functions of quality circle and benefit of quality circles to Employees
- Greater awareness of the organization, organization problems by circle members/Increased knowledge in the area of work
- Greater confidence in tackling issues and generating solutions on the part of circle members is trained.
- Improved productivity and quality because the circles provide checks among the members.
- Improved motivation and self-esteem of the company because of employee involvement in solving organizational problems/concerns
- Improved communication skills.
- Skills development, particularly problem-solving skills.
- Employees become agents of change-making the change process more manageable.
Objectives of Quality Circles
The top broad objectives of the Quality Circle are:
(i) To improve quality, productivity, safety, and cost reduction.
(ii) To give a chance to the employees to use their wisdom and creativity.
(iii) To encourage team spirit, cohesive culture among different levels and sections of the employees.
(iv) To promote self and mutual development, including leadership quality,
(v) To fulfill the self-esteem and motivational needs of employees.
(vi) To improve the quality of work-life of employees.
The benefits of QC circles are as follows:
1) Quality Circle Process helps improved human relations.
(2) Quality Circle Process helps Individual development.
(3) Quality Circle Process helps Leadership development
💥🎁 New Year & Easter Deals On Amazon !
Don't miss out on the best discounts and top-rated products available right now!
🛒 Shop Now and Save Big Today!*As an Amazon Associate, I earn from qualifying purchases.
(4) Improved Work satisfaction through creativity.
(5) Improved awareness of problems.
(6) Quality Circle Process helps strengthened teamwork.
(7) Quality Circle Process helps improved participation.
(8) Quality Circle Process helps Improved willingness to work and take responsibility.
(9) Quality Circle Process helps improved organizational climate.
Advantages of Quality Circles
- Quality Circle Promotion of teamwork
- Quality Circle develops positive employee attitudes.
- Quality Circle creates a positive working environment
- Quality Circle increases quality and productivity
Disadvantages of Quality Circles
- If not addressed, the staff /employees not sure of the purpose
- Not enough relevant training
- Quality circles (QC) are not empowered to make decisions
- Participation not voluntary
- There is little or no management support