Lean Six Sigma Pareto Chart | Pareto Chart Example With Explanation
Pareto principle and Six Sigma and quality management
Pareto principle is the famous 80/20 rule. It’s the idea that things like 80% of the complaints come from 20% of the customers and in the words of Joseph Juran, it’s that there is a vital few things that have the vast majority of the impact and all the rest of the things of the trivial many.
The Pareto principle’s key idea is that a small number of things lead to the vast majority of the result.
The Pareto principle was developed by the quality guru Joseph Juran in 1940, inspired by the work of Pareto, the 19th-century economist.
Vilfredo Pareto observed that in Italy, around the end of 18 century, about 80% of the land was owned by about 20% of the people. At the time, about 80% of the country’s wealth was owned by 20% of the people.
What Juran did was take this idea and apply it in the context of quality control and manufacturing.
The traditional or standard application of the Pareto principle is that 80% of the defects are due to 20% of the causes. That is, a small number of causes are responsible for the vast majority of the defects.
When you look at a process and the potential causes of defects for that process, the vast majority of the defects will be due to a tiny number of possible causes.
Lean Six Sigma Pareto Chart
The Pareto Principle is important for Lean Six Sigma practitioners to analyze the most crucial processes within an organization and identify problems that will result from a small number of causes. The Pareto Chart provides additional detail by displaying the causes of defects and showing how often these defects occur or how much they cost.
This is the idea that’s taught in all quality focused course and training. It’s absolutely standard in the area of quality management and six sigma.
💥🎁 New Year & Easter Deals On Amazon !
Don't miss out on the best discounts and top-rated products available right now!
🛒 Shop Now and Save Big Today!*As an Amazon Associate, I earn from qualifying purchases.
Ishikawa 7 Basic Tools of Quality
Juran created a diagram or chart to go along with this idea of the Pareto principle, and the Pareto chart is one of the seven basic quality tools. The tools include;
-
Cause-and-effect diagram (also called Ishikawa or fishbone diagrams)
A cause-and-effect diagram identifies many possible causes for an effect or problem and sorts possible causes into useful categories.
-
Check sheet
A check sheet is a structured, prepared form for collecting and analyzing data, a generic tool that can be adapted for a wide variety of purposes.
-
Control chart
A control chart is a graph used to study how a process changes over time. Comparing current data to historical control limits leads to conclusions about whether the process variation is consistent (in control) or is unpredictable (out of control, affected by special causes of variation).
-
Histogram
The most commonly used graph for showing frequency distributions, or how often each different value in a data set occurs.
-
Pareto chart
Pareto Chart is a bar graph that shows which factors are more significant.
-
Scatter diagram
Scatter diagrams are graphs of numerical data pairs, one variable on each axis, to look for a relationship.
-
Stratification
Stratification is a technique that separates data gathered from a variety of sources so that patterns can be seen (some lists replace stratification.
The Pareto Principle | Lean Six Sigma
💥🎁 New Year & Easter Deals On Amazon !
Don't miss out on the best discounts and top-rated products available right now!
🛒 Shop Now and Save Big Today!*As an Amazon Associate, I earn from qualifying purchases.
Pareto Chart Example With Explanation
A Pareto chart is a bar graph with one bar for each of the possible categories of causes. These bars are then ordered by frequency, from the most frequent to the least frequent.
The most important cause goes first, and in addition to this chart, the cumulative distribution is usually also drawn.
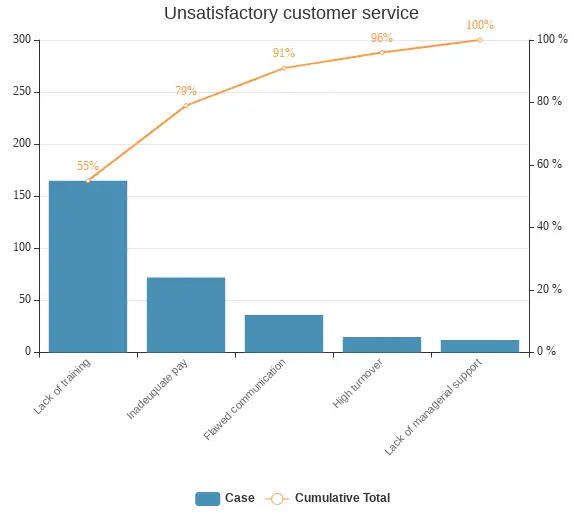
Here is an example that is constructed to show causes of unsatisfactory customer service among the employees
What you can see is that we have a list of possible causes.
- Lack of training
- Lack of adequate pay
- Flawed communication
- High turn over
- Lack of Managerial support
These factors are plotted in the bar graph the percentage contribution to the problem of unsatisfactory customer service.
You can either plot the number or plot the percentage, and those bars have now been ordered by the most frequent.
In this chart, we can see that lack of training is the leading cause of the problem of unsatisfactory customer service. Next and then issues relating to lack of adequate pay.
But the basic idea of the Pareto principle is that 20% of these causes will result in 80% of unsatisfactory customer service.
Now, also, on this chart, there are plotted the cumulative distribution. For example, the top two causes here relate to about 79% of the unsatisfactory customer service.
💥🎁 New Year & Easter Deals On Amazon !
Don't miss out on the best discounts and top-rated products available right now!
🛒 Shop Now and Save Big Today!*As an Amazon Associate, I earn from qualifying purchases.
The top three causes are approaching looks like about 91% and so on. This line is just a cumulative distribution of the causes and shows you essentially what the Pareto chart is, and it’s an essential quality tool.
How do we use Pareto Chart?
It is used to show the most important causes clearly, and in doing and therefore, it’s used to set priorities. This means that the focus of any improvement effort or defect reduction effort should usually be on the first category.
The first category is the most frequent category and, therefore generally, the most important category.
Once you focused on the most important category and it is either eliminated or dramatically reduced, then the parade of principle typically will apply to the remaining categories. So you’re going to move on to the next most important category and so on.
How do we use Pareto in General Life?
But the Pareto principle’s real power extends far beyond just eliminating defects in a process or ranking the most important causes. The Pareto principle’s real power is that it is an abstract idea about a few things causing the vast majority.
It’s widely applicable. In fact, it’s really quite incredible how often this idea applies in real life.
It brings the idea and importance of Pereto thinking.
What is Pareto thinking?
Pareto thinking is that a small number of things are responsible for the vast majority of the result. This is profoundly important.
The Pareto principle allows it really demands to focus on the vital few. In doing so, this provides a great deal of simplification. Then, finally, that focus on simplification results in a great deal of clarity.
💥🎁 New Year & Easter Deals On Amazon !
Don't miss out on the best discounts and top-rated products available right now!
🛒 Shop Now and Save Big Today!*As an Amazon Associate, I earn from qualifying purchases.
Applications in the context of Six Sigma
Within an organization, a small number of processes will be responsible for the vast majority of the organization’s performance.
For example, if you’re beginning to implement process-oriented management for the first time, you need to identify that small number of processes that give you the biggest bang for the buck, and that’s where you’re going to begin to implement process-oriented ideas.
Within a process, you only need a small number of metrics because a small number of measurements will give you the vast majority of the information you need to control the process.
Even within a process of a small number of the process steps are going to be the most important and are going to be responsible for the vast majority of the result.
For example, the vast majority of customer satisfaction as capture above.
The vast majority of the work falls into a small number of categories, and this means that the work in a small number of categories can be cast into processes.
This is because they happen relatively frequently, and there are a small number of them and the amount of the work that doesn’t fall into those categories, which will only be 20% of the work that will have to be handled on a custom basis.
Pareto Principle Examples in Business
- Most businesses have 80% of their profits driven by 20% of their products. Again, about 20% of their customers generate 80% of the total sales.
- 80 % of the errors and defects in the product are caused by 20% of your processes. If you fix that one process, you can achieve outsized results.
- About 20% of the improvement projects will generate about 80% of the savings.
- About 80% of the participation on improvement teams will be due to 20% of the employees.
- A small number of your suppliers will cause the vast majority of your problems, and the idea goes on and on and on.
It’s just so widely applicable throughout Six Sigma and the ideas of Six Sigma and really throughout the business.